Expert Engineering Reports for Comprehensive Seawall Inspections, Repairs, and Full Construction.
Bulkhead Inspection: Why It Matters and How to Do It Right
Blog post description.
11/25/20243 min read
Introduction
When it comes to protecting waterfront properties, bulkheads play a crucial role. Acting as barriers between land and water, these structures prevent erosion, flooding, and damage. However, like any structure exposed to natural forces, bulkheads require regular inspections to ensure they remain in good condition.
In this article, we'll dive into everything you need to know about bulkhead inspections—why they're essential, what they involve, and how to address issues before they escalate.
What Is a Bulkhead?
Definition and Function
A bulkhead is a retaining wall designed to prevent soil erosion and protect properties from the encroachment of water. These structures are often constructed using materials like wood, concrete, or vinyl.
Common Locations of Bulkheads
You’ll typically find bulkheads along shorelines, marinas, and waterfront properties. They serve as the first line of defense against tides, waves, and storm surges.
Why Are Bulkhead Inspections Necessary?
Protecting Property from Water Damage
Without a sturdy bulkhead, water can wreak havoc, leading to erosion, flooding, and structural instability.
Ensuring Structural Integrity
Inspections help identify weak points that may compromise the bulkhead’s ability to function effectively.
Compliance with Local Regulations
Many regions have strict requirements for bulkhead maintenance and inspections, especially in areas prone to hurricanes or heavy storms.
Signs That a Bulkhead Needs Inspection
Visible Cracks and Damage: These can indicate structural weakening.
Water Seepage and Leakage: A sign of compromised seals or materials.
Erosion Around the Bulkhead: Suggests that water is bypassing the structure.
Key Components of a Bulkhead Inspection
Assessing Structural Integrity
Inspectors check for cracks, warping, or leaning that might affect the bulkhead’s performance.
Checking for Corrosion
Metal components, such as tie rods, are prone to rust and need careful evaluation.
Evaluating Connections and Fastenings
Loose or broken fastenings can weaken the bulkhead's overall stability.
How Often Should Bulkhead Inspections Be Conducted?
The frequency depends on factors like age, material, and exposure to environmental conditions. Generally, annual inspections are recommended, but high-risk areas may require more frequent evaluations.
The Role of Professional Inspectors
Expertise in Identifying Issues
Professionals can spot problems that might not be visible to the untrained eye.
Using Advanced Tools and Techniques
From sonar imaging to underwater cameras, professionals utilize technology to inspect hard-to-reach areas.
DIY Bulkhead Inspections: What to Look For
Basic Visual Checks
Look for cracks, discoloration, or signs of wear and tear.
Safety Precautions for Homeowners
Always wear protective gear and avoid venturing into unstable areas.
Common Bulkhead Problems and Their Solutions
Erosion and Washouts: Addressed through proper drainage systems.
Material Deterioration: Repair or replace damaged sections.
Misaligned Panels: Realignment may be necessary to restore functionality.
Advanced Techniques for Bulkhead Inspections
Underwater Inspections
These help assess submerged portions of the bulkhead.
Use of Sonar and Imaging Technology
High-tech tools provide detailed insights into structural conditions.
Bulkhead Repair vs. Replacement
When to Opt for Repairs
Minor issues like small cracks or localized damage can often be fixed.
Indicators for Replacement
Extensive damage or failure to meet safety standards typically warrants replacement.
Costs Associated with Bulkhead Inspections
Inspection fees can range from $300 to $900, depending on the complexity and location. Repairs, on the other hand, vary widely based on the extent of the damage.
Importance of Documentation in Bulkhead Inspections
Keeping detailed records is vital for insurance claims and future maintenance planning. These documents can serve as proof of diligence in property upkeep.
Tips for Hiring a Bulkhead Inspection Service
What to Look For in a Contractor
Choose a licensed and experienced professional with a strong reputation.
Questions to Ask Before Hiring
Do you use advanced inspection tools?
Can you provide references?
What’s your experience with bulkheads in this area?
Conclusion
Regular bulkhead inspections are non-negotiable if you want to protect your property from the elements. By identifying and addressing problems early, you can save yourself significant time, money, and stress in the long run. Don't wait for visible damage—schedule an inspection today.
FAQs
What is the average lifespan of a bulkhead?
Depending on the material, bulkheads can last 20–50 years with proper maintenance.How much does a typical bulkhead inspection cost?
Inspections usually cost between $500 and $1500, depending on location and complexity.Can I inspect my bulkhead without professional help?
Yes, but professional inspections are more thorough and reliable.What are the most common materials used for bulkheads?
Wood, concrete, and vinyl are the most common.How do weather conditions affect bulkhead inspections?
Stormy weather can accelerate damage, making frequent inspections crucial.
© 2012-2024 Souffront Contractors & Engineers | All Rights Reserved
Estimates@souffrontcontractors.com
Phone: 877-420-7220
© 2024. All rights reserved.
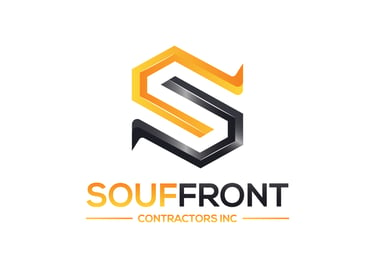
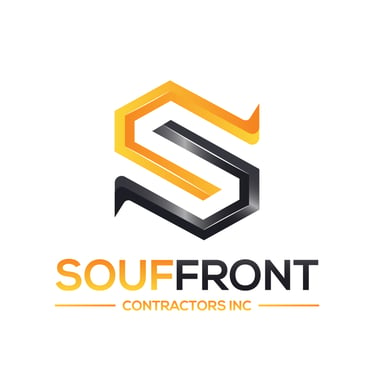