Expert Engineering Reports for Comprehensive Seawall Inspections, Repairs, and Full Construction.
Restoring a Very Old Seawall Using an Overpour Method and Modern Reinforcement Techniques
Restoring a Very Old Seawall Using an Overpour Method
1/11/20253 min read
Restoring a Very Old Seawall Using an Overpour Method and Modern Reinforcement Techniques
When dealing with an aging seawall, especially one showing signs of cracking, spalling, or structural fatigue, employing modern restoration techniques can provide renewed strength and durability. Below, I outline a strategy using the overpour method, quadrilling for digging at intervals, installing 2-inch steel pin pilings, and integrating a rebar cage into the new seawall cap.
Understanding the Challenges of an Old Seawall
Older seawalls often suffer from:
Cracks and spalling in the concrete.
Erosion at the base or toe of the structure.
Corroded reinforcements.
Loss of soil behind the wall due to improper drainage.
Restoration focuses on addressing these deficiencies to ensure the seawall withstands modern environmental challenges, such as sea-level rise and tidal forces.
Step-by-Step Process
1. Initial Assessment and Preparation
Inspection: Conduct a thorough structural assessment using visual and underwater inspections. Document cracks, erosion, and any failing sections of the wall​​.
Permits and Compliance: Obtain necessary permits from local authorities to comply with modern codes, such as the "Resiliency Standards for Tidal Flood Protection" ordinance​​.
2. Overpour Technique for a New Seawall Cap
Surface Preparation:
Clean the existing seawall surface by scraping away marine growth and pressure washing​​.
Repair major cracks using epoxy injection or hydraulic repair mortar​​.
Overpour Application:
Construct formwork around the existing seawall cap to accommodate the overpour.
Use high-strength, marine-grade concrete (minimum 5,000 psi)​​.
Pour the concrete to create a new, raised seawall cap with chamfered edges for durability and aesthetics.
3. Quadrilling for Pin Piling Installation
Drilling at Intervals:
Use quadrilling techniques to drill evenly spaced cores (e.g., every 8 feet) through the existing cap​.
This ensures the integration of reinforcement without compromising the structural integrity of the seawall.
Driving Pin Pilings:
Install 2-inch steel pin pilings into the drilled holes. These pilings should extend deep into the substrate for stability.
Use corrosion-resistant coatings on the steel to prolong its lifespan.
4. Integrating Rebar Cage into the New Cap
Reinforcement Setup:
Place a rebar cage within the formwork for the new cap. Ensure the steel is tied securely to the pin pilings​.
Add supplementary tiebacks or anchors for additional stability, as necessary​.
Pouring the Cap:
Encapsulate the rebar cage with the marine-grade concrete during the overpour. This integration strengthens the seawall cap and ensures the new section bonds with the old structure.
5. Addressing Drainage and Erosion
Install Drainage Features:
Incorporate jet filter systems to manage hydrostatic pressure and prevent soil loss behind the seawall​​.
Stabilizing the Toe:
Add a concrete footer or additional material to stabilize the seawall's base if erosion has compromised its integrity​.
Practical Tips for Seawall Restoration
Schedule work during low tide to maximize visibility and efficiency.
Use marine-grade materials designed to withstand saltwater environments​.
Regularly inspect the repaired seawall for new cracks or signs of wear​​.
FAQs About Seawall Restoration
Q1. What is the lifespan of a repaired seawall?
A properly restored seawall, using marine-grade materials and modern techniques, can last 30–50 years depending on environmental conditions.
Q2. How does overpouring improve seawall durability?
Overpouring adds structural integrity to the seawall cap by reinforcing it with a new, thicker concrete layer and integrating rebar.
Q3. Why are drainage systems critical?
Drainage systems prevent hydrostatic pressure buildup, which can lead to cracks and eventual failure of the seawall​.
Q4. How much does this process cost?
Costs vary based on linear footage and materials but can range from $350–$600 per linear foot for overpouring and pilings​.
Q5. Are permits necessary for seawall repair?
Yes, permits ensure compliance with local ordinances and environmental standards, protecting property owners from legal issues​​.
For seawall inspections, repairs, or new construction, contact Souffront Contractors Inc. at 305-219-9970 or visit Souffront Contractors Inc.. Let us help you protect your waterfront property with expert solutions tailored to your need. Check Out This Article
© 2012-2024 Souffront Contractors & Engineers | All Rights Reserved
Estimates@souffrontcontractors.com
Phone: 877-420-7220
© 2024. All rights reserved.
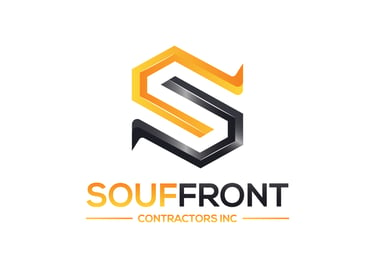
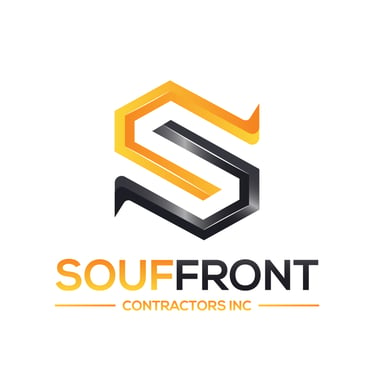